
ASCENT ABORT
Optimization
In an effort to develop and improve my thrust vector controlled rockets, it's important to optimize every part in the rocket. Every gram of weight removes performance from the rocket. Enter Ascent Abort, The smallest possible to make a fully functional TVC Rocket.

The real Rocket
Miniaturization
At 1/50 scale version of the Orion Ascent Abort allowed me to use the same 98mm tube I had used for my SLS. I worked to reduce the weight of the thrust vector control system using the info I had learned building my SLS. The weight was reduced by about 30% from the version installed in the SLS. The Avionics were also minimized to reduce weight and vertical height. All in all the vehicle has only 200mm of usable space for electronics and mechanical parts in the aeroshell.

The Model

Internals
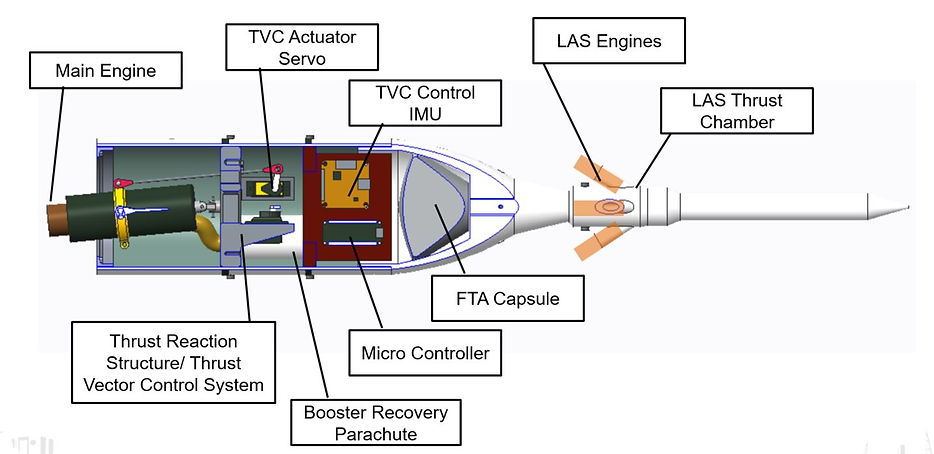



TESTING
As with anything unproven or new, The Ascent Abort needed to be tested before I had enough confidence to let it fly. Several things in sequence had to go right:
-
The Vehicle had to receive the launch signal and leave standby mode
-
The Vehicle cannot trigger pyrotechnics while in standby mode
-
The Vehicle must be able to trigger the on-board pyrotechnics under internal power
-
The vehicle must be able to move the TVC System in the correct direction to counter the rockets movement in flight
-
The Nose cone must be able to separate and eject the parachute in the process
All of the above criteria must be executed by the rocket to have a fully successfully flight.
testing the electronics and software was relatively easy but still needed several revisions to ensure the vehicle didnt try to launch inadvertantly or trigger the recovery system too early.

On the whole getting the recovery system to work on this rocket was the hardest part. It demands 4 engines fire in unison to remove the nose cone. The first iteration intended to solve this with a reverse nozzle using a single engine like the real thing but the thrust was too reduced and the engine would destroy the nose of the rocket after the ejection charge fired (pictured above)
the real vehicle
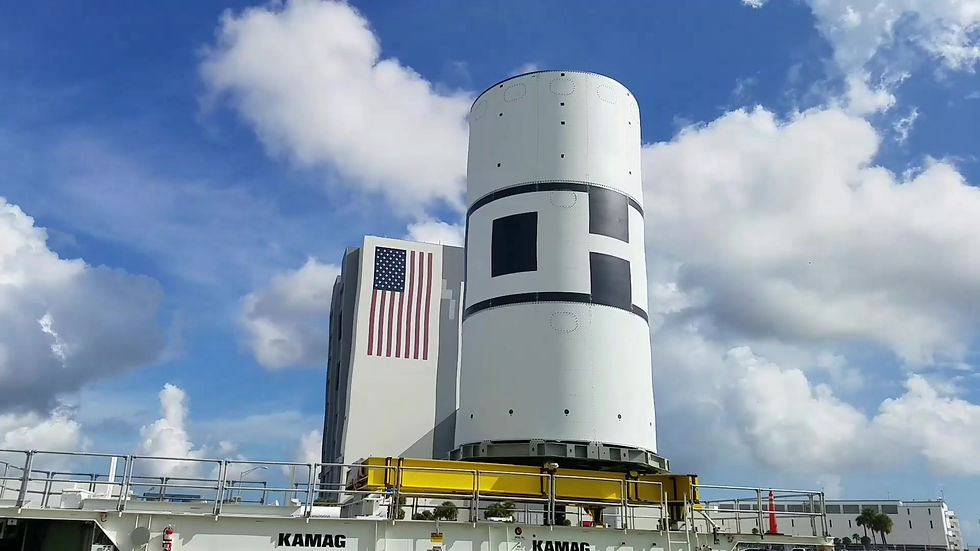
MININIATURE
One of the perks of working at the space center is you can occasionally go see real flight hardware and if you're lucky enough to know the owner of that hardware, you can go take pictures with it.
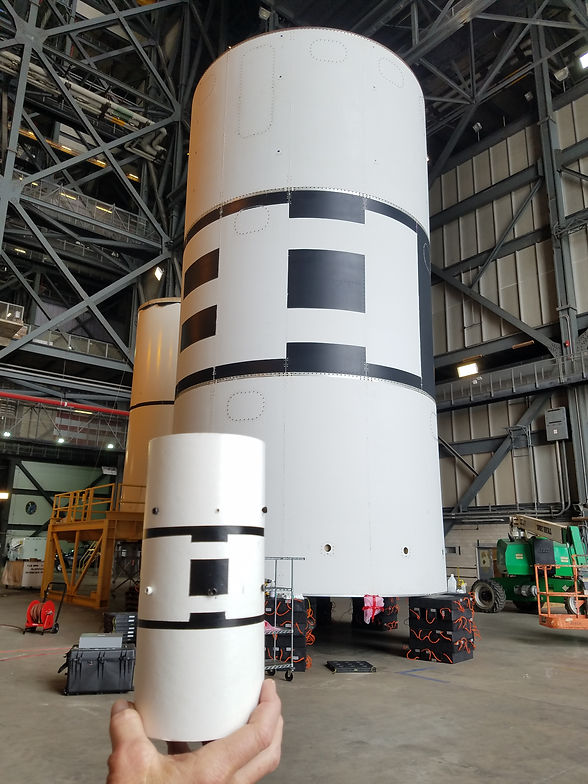
1ST FLIGHT TEST
Eventually it came time to try a full up flight test of the vehicle. After many set backs, misfires, and struggles it came time to send it skyward. The flight demonstrates a mixed bag of success. A rocket this short and stubby should not be able to fly at all but due to the stabilization it can- although the control gains on the PID loop were a bit over aggressive. The rocket was able to correct back to center several times but entered a control induced oscillation that eventually led to it flipping off axis right before trying to deploy the parachutes. It was not successful in doing so... Overall these issued have been dealt with in anticipation of the next flight test!
FLIGHT TEST -1
